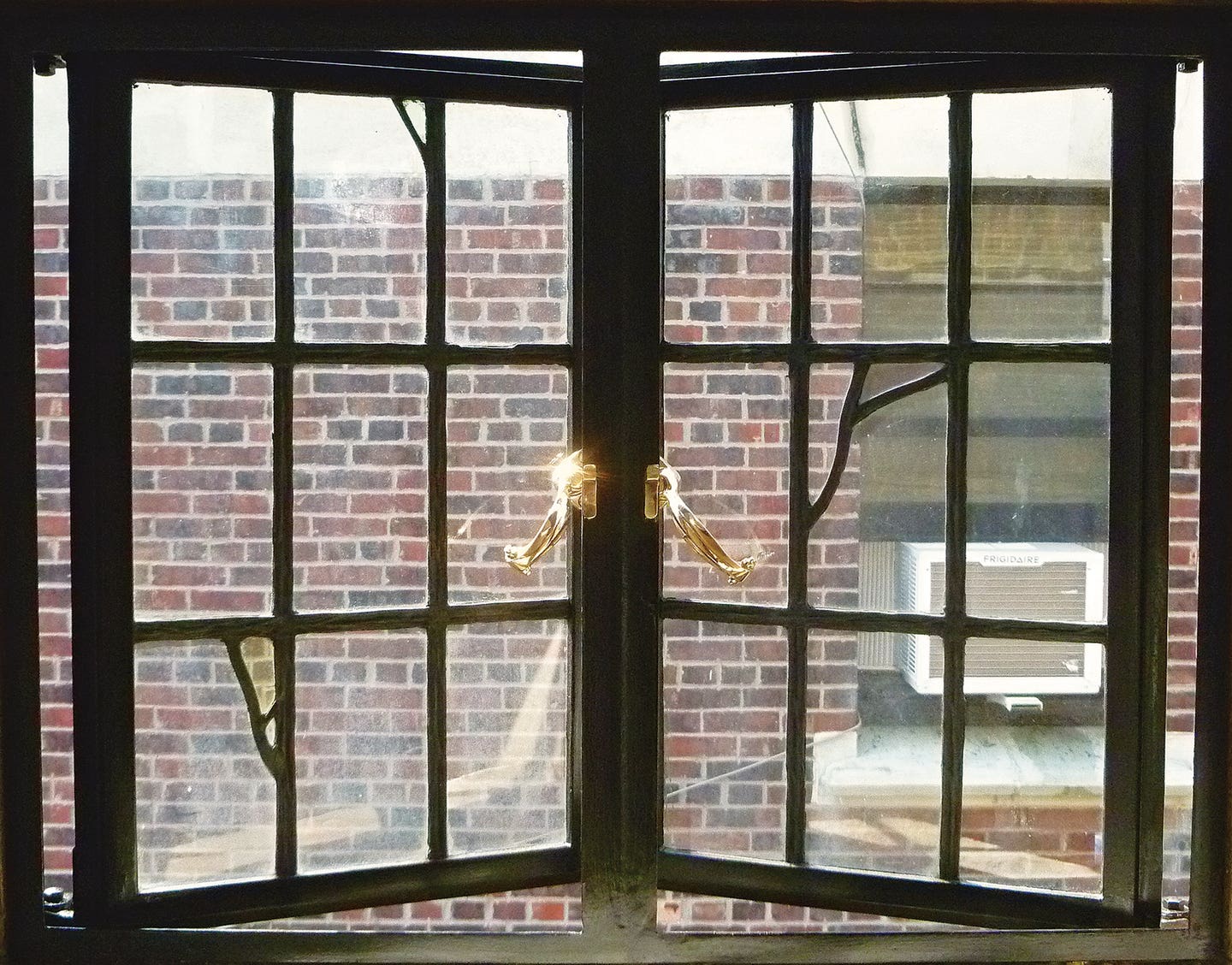
Making Sense of Metal Windows in Historic Buildings
Steel windows remain hard at work in thousands of institutional and commercial buildings of the 1910s, ’20s, ’30s and early ‘40s, but given that they were scarce before the late 19th century, the reason for their ubiquity is not as obvious. “In its heyday, the steel window wasn’t a trend or fashion,” says Darren Joyce of Crittall Windows, Ltd. in Witham, UK, “it was a window of necessity.” As he explains, until mild steel became widely available in the 1890s, the only materials for windows were wrought iron (traditionally made into windows in the UK by local blacksmiths) and, of course, wood. “Steel windows offered massive advantages for making large windows, and in the Art Deco and Modernist periods, architects loved them for their design flexibility.”
The first step in attempting to match steel windows from an earlier era for either sensitive rehabilitation or additions is to understand what you have. By the 1920s, more than a dozen domestic and international manufacturers were in the market, using a wide variety of metal bar profiles or sections. “Most likely your existing bar profiles are either in the Universal Range,” explains Joyce, “or, if they have been replaced from 1964 onwards, they’re probably from the W20 range.”
Bars from the SMW (Standard Metal Window) range, used for light commercial buildings and residential windows, are still in production. “However, if your windows are in an institutional or commercial building, they’re most likely to be from the Universal Range, therefore the windows that you would consider today for a match are in the W20 range.” Though the W20 range of bar profiles is similar to the Universal Range (being based on them), if they’re not close enough the game isn’t over. “To exactly match the existing sightlines,” which Joyce notes are critical for many historic preservation projects, “we can laser-cut down profiles.”
Learn more about historic steel window profiles and manufacturing process: The History of Steel Windows
Equally characteristic are the glazing bars or muntins, which have two defining elements. “One is the overall sightline of the metal you see,” explains Joyce, “and the other is the profile of the bar.” A lot of existing metal muntins are a simple T-profile – that is, just a flat bar on one side of the window (inside or outside) and two glazing rebates (recesses) on the other side. “However, a lot of earlier windows had muntins with ornately curved profiles, sometimes called a Queen Anne section or a lamb’s tongue profile.” No surprise, the more ornate muntins can be hit-or-miss to match, but T-profile muntins with flat bars are easy to replicate in mild steel, he says.
Upgrading to Today's Energy Efficiency Standards
As with traditional wood windows, what makes matching the appearance of historic sightlines trickier is trying to also include energy conservation upgrades, especially with true divided lights. Explains Domenick Siano of Steel Windows and Doors in Stratford, CT. “In today’s frame systems, you are typically using an insulated glass unit (IGU), which is much thicker than single pane glass and can reduce the exterior surface for applying putty, but still can be done with deeper sections.”
Joyce adds that in such cases the W20 range may be an option. “We have other window ranges as well with a wider front-to-back dimension so it’s possible to set the glass back into the frame like the existing windows, and maintain the same visible putty slope on the exterior of the building.” Added to this is the double seal and spacer bar around the IGU that needs to be hidden from view. “The most popular historic muntin widths were ¾-, 1-, and 11/8-in., though there were many intermediate sizes,” says Joyce. Since there’s a limit to how low the spacer bars in an IGU can be made, the choice for a steel muntin bar that still hides the seal and spacer usually winds up about 11/8-in.
In addition to true divided lights, Joyce says that on a project-by-project basis they can make simulated divided lights (SDL) with a steel welded grid. “This way, you have one insulated glass unit, and a much thinner muntin grid layout to replicate existing windows.” Adds Siano, “With an SDL you have a better performing window because you have one glass unit, versus say six, nine, or twelve pieces of glass on a unit, it provides a better center of U value with one large piece equating to a better performing unit; plus there are scores of glass make-ups available with specialty coatings which help increase the performance.”
Moreover, it’s also possible to emulate the leaded glass panels used in many earlier romantic-style steel windows. As an example, Siano describes a recent commission for a new project designed to look like a historic building. “We’ve made a custom profile specifically for this project, but stretched front-to-back to allow for a triple glazing.” To the exterior of the interior high performance IGU is a true leaded glass panel separated by a specially vented gap. “So this window has very low U-values, and very high wind, water, and air penetration resistance performance level, but from the street it’s historically accurate to the original 1920s and ‘30s windows on the site.”
Other advances in steel windows include polyester powder-coating, which is designed to reduce maintenance to little more than periodic washing. However, Joyce says the biggest improvement – and one that doesn’t alter the aesthetic of the window – is hot-dip galvanizing. “Older windows, if kept painted every six or seven years, are never going to rust, but in reality that doesn’t happen.” Hot-dip galvanizing is a bit of a black art to really get correct, he says, “but we’ve been doing the process for over 60 years, so we’re pretty good at it.”
Historic Aluminum Windows
Aluminum, another metal widely used for windows, appeared as early as the 1930s, but did not really edge out wood and steel until the latter 1940s and the post-World-War II building boom. “We started making little hopper-vent aluminum windows for bathrooms and glass block walls in the 1940s and ‘50s,” says Kurtis Suellentrop of Winco Window Company in St. Louis, MO, “but I would say aluminum windows have only been common in commercial buildings since the 1960s.”
No doubt, ample manufacturing capacity left over from producing aircraft and other war materiel helped boost the availability of aluminum windows, but the metal itself also offered many advantages. Rather than being rolled like steel, aluminum window parts are extruded (pushed or pulled) from dies – not unlike a child’s Play-Doh toy – a process that makes possible hollow elements in far more elaborate shapes.
Suellentrop says aluminum is one of the most adaptable materials for making custom shapes. “We obviously have to create dies and tooling for the window parts, and to prep and cut that material, but new extrusions are relatively easy to produce, especially if they’re trim.” Adds William True of True Enterprises, Inc. and Winco, “If the client is interested in materials that have been recycled – say, for a LEED project – about 80% of the aluminum now in our products is recycled. Also, there isn’t much upkeep on an aluminum window, which can be finished with either a 70% Kynar coating or anodizing in different colors.”
True and Suellentrop agree that aluminum’s versatility makes it well-suited to matching the construction and appearance of wood and steel windows, which is the bulk of their historical window business. However, though replicating original, historic aluminum window sightlines, profiles, and aesthetics, is even easier, it’s typically not as simple as just cloning the originals. “If you’re in a high wind-load situation, you may need to reinforce the aluminum,” explains True. “Perhaps you put more aluminum towards the face of the window so it builds it up, or add steel hidden from the outward appearance. Replacing windows can mean you have to bring them up to today’s codes.”
A textbook example of a historic aluminum window project that went beyond mere replication is the Walter Gropius-designed JFK Federal Building in Boston, dedicated in 1966. “The windows were originally aluminum, but single-pane and not bomb-blast resistant,” says Suellentrop. “We upgraded them to not only be more thermally efficient but also to protect the occupants in case of an explosion.” Upgrades it turns out were not just in the glass or doubling up the panes. “We made significant increases in the thickness of the aluminum, and even had to use a higher-strength alloy in order to meet the blast codes, sometimes with steel reinforcement.”
In fact, one of the biggest issues with a historical aluminum window project may not be the window itself but the planning. Says Suellentrop, “If we’re trying to match a historic building, we need to plan on the lead time for the production, especially if it takes custom dies. I always stress early involvement because, if we can look at the design, do mock-ups, and even test the installation early-on, then we have time to react and make those custom shapes.”
Designing fastener installation is a particularly important part of planning for historic renovation projects. “Buildings from 50 or 100 years ago were not necessarily designed to withstand the installations that we’re required to meet on the current code, so we really like to be involved early on to be able to remove the old window and do some fastener pull testing.”
He describes such a project on a 100-year-old building at Fort Riley, KS, for the First Infantry Division. “The construction was a split-face limestone on the exterior and limestone block on the interior, but in-between was just infill of rubble, cigarette butts, clippings -- literally whatever else they had. So months in advance we had to go in there and design a system of steel and grout that would withstand the loads needed for blast-resistant windows.” He says six to 12 months lead time is typical for such planning. “In the JFK Building, a large, complex project, we were designing for probably 18 months – doing a lot of mock-ups and testing, going back and forth with the glass factory, and so on.”
Fortunately, the mock-up process is also changing with the times. “We’re into 3-D printing now,” says True, “where you can mock-up something out of plastic, bring to the job site for comment, then reproduce it in aluminum.” Suellentrop adds that rather than waiting two or three months for a sample of the extrusion – and paying for the costs of the tooling -- it’s now possible to draw it in three dimensions and print it out. “We may even paint it and insert glass to show how the completed window will look,” he says. “If there are any issues, they’ll be a lot easier to fix in plastic and paper than metal.”
Gordon Bock lists his seminars, keynote lectures and workshops at www.gordonbock.com.
Gordon H. Bock is an architectural historian, instructor with the National Preservation Institute, and speaker through www.gordonbock.com.