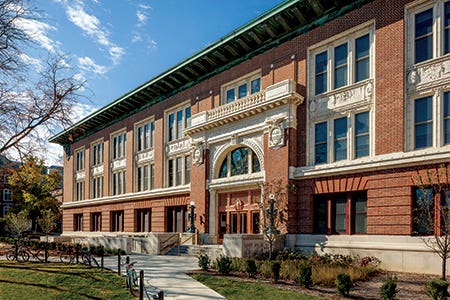
Lincoln Hall at University of Illinois is Restored
PROJECT: Lincoln Hall, University of Illinois at Urbana-Champaign, Champaign, IL
PROJECT ARCHITECT: CannonDesign, New York, NY
ASSOCIATE ARCHITECT: Bailey Edward, Chicago, IL; Robin Edward Whitehurst, AIA, LEED AP, principal-in-charge; Susan Turner, AIA, LEED AP, PMP, historic preservation leader and project manager
GENERAL CONTRACTOR: Williams Brothers Construction Co., Inc., Houston, TX
LEED: Platinum
While most students at the University of Illinois at Urbana-Champaign (UIUC) will eventually attend a class in Lincoln Hall, home to the College of Liberal Arts and Sciences, few would have stopped to admire the artistic and historic details on the building, until now. The 100-year-old, four-story structure has recently undergone a $40-million rehabilitation and restoration lead by CannonDesign of New York, NY, with Bailey Edward of Chicago, IL, acting as associate architect. Project goals included the restoration of historic spaces, complete rehabilitation of the building interior to provide 21st-century education environments, additions to accommodate the school’s growing programs and mechanical systems upgrades that didn’t interfere with the building’s historic fabric, and all while aiming to achieve LEED gold status.
“As associate architect, our primary task was the historic preservation elements,” says Robin Whitehurst, principal-in-charge at Bailey Edward. “That includes the building exterior, significant interior spaces that were historic as well as working very closely with the entire design team with integrating infrastructure systems in an appropriate way that would meet the Secretary of Interior’s Standards for Rehabilitation.”
Lincoln Hall was built in 1912 to commemorate President Abraham Lincoln. An example of Neoclassical architecture, the building also features Prairie style influence with its large 5-ft. bracketed copper overhang, terra-cotta bas-relief plaques along the east and south elevations that depict scenes from President Lincoln’s life and a limestone watercourse. In 1927, an addition was built on the rear to create what Whitehurst describes as a square “doughnut” shape with an auditorium at the very center that allowed for two courtyards, one on either side.
“When they built the addition, the design tried to match the original building as closely as possible in terms of material and detailing on the exterior,” says Whitehurst. “In the interior, the design went a different direction. The designer at the time was exploring new materials for the addition. That’s why the spaces weren’t restored to one time period but rather to their original respective dates. We were consulting with the Illinois Historic Preservation Agency and Melvyn Skavarla, the campus preservation officer, throughout the project to ensure accuracy.”
A comprehensive feasibility study was conducted and from an historic preservation standpoint that meant thoroughly understanding the history of the building, the materials used and its present conditions, and to research the appropriate methodology to restore them. Among other things, the study found that the brick exterior required repointing. “We discovered that the college had done a ‘Mass Grouting’ campaign in the 1970s where they treated the brick repointing as if it was a tile project,” says Whitehurst. “They taped the face of the brick and smeared mortar into the joints. We found pieces of tape still embedded in the mortar, which was how we unraveled what they had done. Unfortunately, a very high Portland content mortar was used and the removal of that material became very difficult.”
To ensure that the brick repointing would appear uniform, Whitehurst and Susan Turner, historic preservation leader and project manager at Bailey Edward, specified that all of the masons at Mid-Continental Restoration Co. of Fort Scott, KS, the firm responsible for masonry restoration, as well as the Bailey Edward team, attend a two-week class on how to correctly repoint historic masonry. After the repointing was completed, the bricks were cleaned with Vana Trol, manufactured by Prosoco of Lawrence, KS. “Our staff took the course so that we could evaluate if the masons’ techniques were appropriate to achieve the results that we needed,” says Whitehurst. Karla Smalley, AIA, LEED AP of Bailey Edward, served as the project’s on-site architect and construction observer. She was available to review each of the eight contractors’ work and provide design direction when required.
The study also found that the terra-cotta bas-relief panels were in poor condition. There was crazing in the glaze and some portions had fallen off. However, rather than replacing damaged pieces, the team took an art conservation approach to preserve them. Edison Coatings of Plainville, CT, manufactured the coating that was applied to all of the terra-cotta elements on the exterior.
The Best Approach
To determine the best sustainable approach for the windows, Bailey Edward conducted an in-depth study to examine the comparative efficacy of whether to restore or replace existing windows. “We did four physical mock-ups of these very large double-hung wood windows,” says Turner. “We used an exterior storm window, a brand-new wood-clad aluminum window that looked like the original, a restored window upgraded with thermal glazing and tested them against an existing window to determine the capital cost, operational cost and maintenance cost.
“We found that the restored window worked well for historic appearances,” continues Turner. “If capital cost is the main concern then the exterior storm window performed very well from a thermal viewpoint and lifecycle costs because initial costs were very expensive, but it performed poorly in terms of maintenance. Interestingly, we found that the restored window outperformed in R-value to the new window but it didn’t outperform relative to air infiltration. In the end, as maintenance cost was the primary driver, UIUC elected to replace the windows with wood-clad aluminum ones [manufactured by Parrett Windows and Doors of Dorchester, WI].”
Inside, the original polychromatic paint scheme in the lobby at the quad entrance, auditorium and corridors were all covered with an institutional green. Anthony Kartsonas, principal of Chicago, IL-based Historic Services conducted a paint analysis to determine the original colors in the historic spaces, in all there were 28 paint colors and 5 different metal leafing. Based upon drawings and specifications completed by Bailey Edward, Koch Brothers Decorating of St. Louis, MO, reinstated the original polychromatic paint scheme, stenciling and leafing throughout. The firm also cleaned and restored the marble columns, wall panels and floor tile in the lobby. A new sprinkler system was installed in the lobby’s barrel vault ceiling; the sprinkler heads were painted to match the polychrome ceiling.
“There are a lot of beautiful historic custom-made light fixtures in this building and each of them had their own challenges because we wanted to restore the original fixtures while providing flexible yet low-energy fixtures,” says Turner. “We worked very closely with the lighting restoration company [Lumenelle of Union, IL] to match existing fixtures in the lobby so that we could get the light levels that are required for an exit space and also to restore and retrofit the existing ones for energy efficiency.”
For the auditorium, Turner was able to find the original glass segments for the basket light fixtures. “Due to seismic concerns, all of the beveled curved glass segments were removed and replaced with translucent plastic, which dramatically altered the light quality” she says. “By venturing into the attic spaces above to see if we had enough height to retrofit a wall, I located the glass segments. We retrofitted the fixtures with clips for the glass and that resolved the seismic concerns. The fixtures are back to their original appearance.”
The Auditorium
The auditorium’s new function is now a lecture hall as the college was able to designate other areas on campus for theater performances. As a result, the theater’s large cyclorama, a large plaster feature, was documented according to HABS standards and removed for programming space; an asbestos fire curtain painted with a Greek elegy was also documented and removed. New auditorium seating replaced the old ones and the decorative end panels were all cleaned, restored and reinstalled. While the bas-relief plaster medallions on the auditorium walls were never painted over, two of them were missing.
“In the 1920s, composite ornaments came from two locations, Jacobson & Company of New York City and Decorators Supply Corp of Chicago,” says Turner. “The latter actually worked on the project when the auditorium was built. They based the medallions on a Jacobson catalog number so it wasn’t Jacobson products that were installed but copies.” Since replacements are no longer available, Turner and Whitehurst worked with the plaster restoration contractor and Koch Brothers to sculpt and paint new medallions based on historic photographs and the colors used in the extant medallions.
In addition to restoring the historic spaces, the Bailey Edward team worked closely with CannonDesign and the MEP engineer firm KJWW Engineering Consultants of Quad Cities, IL, in implementing new climate control systems, determining the soft spots for ramps and lifts for accessibility and mechanical upgrades for 21st-century classrooms and office spaces. The building envelope was also upgraded with Icynene spray foam insulation. During installation, all of the existing wood trim in the classrooms were removed and reinstalled afterward. “We felt it was inappropriate to upgrade the lobby and auditorium because we’d lose the walls with stenciling, polychromatic paint and three-dimensional plaster,” says Turner. “However, we conducted an energy model to prove that we’ve upgraded the building thermally sufficient so it wasn’t necessary to intervene with the very historic spaces.”
The near-decade-long design and construction process has resulted in the successful restoration and rehabilitation of UIUC’s Lincoln Hall. The project has not only met LEED Gold status but has accrued enough points for LEED Platinum certification. “Where Bailey Edward differentiates itself from other historic preservation firms is that we look at a historic building as if we’re part of the continuity of that building,” says Turner.
“To do this, we work to fully understand how new building codes and standards will impact the building and to fully understand the difference between preservation and sustainability,” she explains. “That means to understand the building envelope design and how to weave sustainability through the design so that they’re not at odds with each other and all the while tailoring the clients’ needs to that balance. One of our pride points is that when we’re finished with preservation, observers don’t know that we were there; it looked as if the building was like that all its life.”