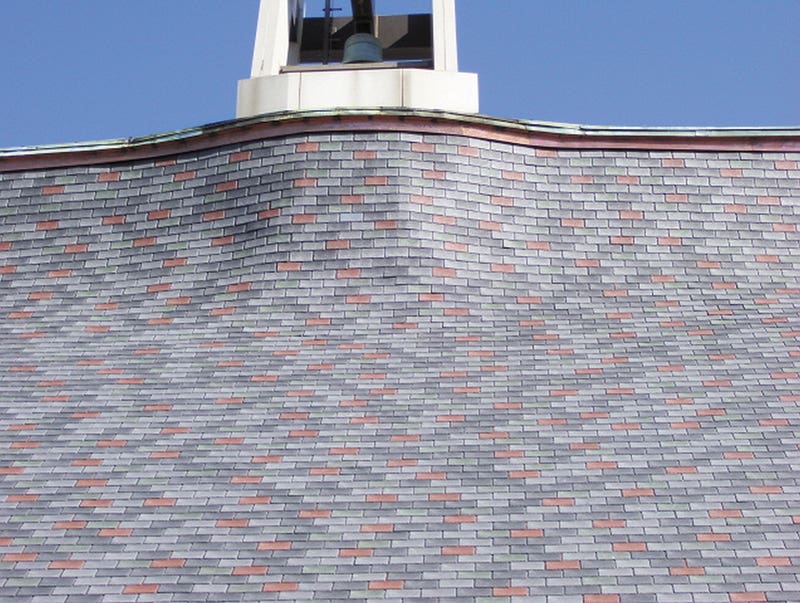
Synthetic Slate Roofing for Churches
Slate roofs have crowned buildings in the United States since the mid-1600s, when European settlers brought the then-centuries-old technique to the New World. Over the past few decades, several manufacturers in the United States have developed simulated-slate roof tiles made from a variety of materials. Two recent re-roofing projects illustrate their practicality and versatility.
Synthetic Slate Roofing at the VA Medical Center Chapel
The Veterans Administration Medical Center in Dayton, OH, was built to meet the needs of Civil War veterans. Not long after the facility opened in 1867, a group of sufficiently able-bodied residents began quarrying limestone on the grounds. The stone blocks were used to build a chapel, which was completed in 1870. One of the most striking features of the stately Gothic building was a roof on which two colors of slate tiles were arranged to form a large cross surrounded by stars.
Eventually, the slate roof was replaced with plain, brown asphalt shingles. When it was time to replace the worn-out shingles, the Veterans Administration decided to re-create the roof’s original appearance. However, the re-roofing project’s architect decided that the current roof structure could not support the weight of natural slate. Synthetic slate tiles offered a viable alternative.
The project team selected synthetic slate made by DaVinci Roofscapes of Kansas City, KS. The DaVinci tiles are made by injecting polymer material into molds made from a variety of natural slate tiles to create authentic variations among the individual tiles. Using a 7½-in. exposure, the installed weight of these synthetic tiles is 273 lbs. per 100 sq.ft., compared with 800–1,000 lbs. for natural slate. Besides putting less of a burden on the structure, that lower weight also reduces the cost of trucking the tiles to the site.
Another reason for selecting DaVinci slate for this project was that the tiles are available in several widths. This proved to be important for producing the cross-and-stars pattern. The only record of the original design was a faded, century-old photograph. It was up to the roofing contractor, Detroit Cornice and Slate Company, to figure out how to duplicate it. “When you want to create a straight line with differing colors of slate, you actually have to have the water slots lined up,” says Dawn Hesse, project manager for the Ferndale, MI, roofing company, “and you can’t have your water slots lined up, because then you won’t have a waterproof roof.”
Typically, Hesse’s crew offset the tile edges by half a tile width, but doing that would have resulted in sawtooth verticals on the cross rather than the desired straight edges. Instead, on the approaches to the cross, the roofers used a combination of 6-, 9- and 12-in.-wide tiles to get as close as possible to straight edges when changing from the background black tiles to the cross’s tan tiles. “We worked with DaVinci, and they were able to maintain the warranty with an inch-and-a-half offset,” Hesse says. DaVinci’s standard warranty is 50 years.
Synthetic Slate Roofing at the United Methodist Church
The United Methodist Church in Kirkwood, a suburb of St. Louis, MO, is a dramatic structure whose exterior is nearly all roof. In the 45 years since it was built, the roof’s asbestos asphalt shingles had deteriorated badly. The church owners considered replacing them with various types of shingles, but decided to use simulated-slate roof tiles made by InSpire Roofing Products of Wixom, MI. These composite tiles are compression molded from a mixture of limestone and resins. “The InSpire was very competitive, was a lot cheaper, and they were very pleased with the way it looked,” says Jim Diehl, vice president of J & S Roofing Technologies of St. Louis. “They duplicate the look of real slate, and when you look at them from the ground up, you can’t really tell the difference.”
The price of artificial slate is higher than asphalt or composite shingles, but less than natural slate. Costs vary by region and by distance from suppliers, but Bill Broeker Jr., vice president of Old Style Roofing of Fenton, MO, estimates that in his market area, simulated slate costs somewhere around 60 percent of natural slate.
The roof’s cost, appearance and durability (InSpire provides a 50-year warranty) were important to the church’s owners. Broeker had another reason for liking the InSpire slate. He explains that, unlike natural slate, the artificial tiles are somewhat flexible, and introducing a longitudinal arch to the tile before nailing it down helps it to hug the roof and resist lifting. InSpire tiles are arched during the manufacturing process. “Most of the [simulated slate] manufacturers’ products are not pre-arched in the mold, so before you nail every one of those down, you’ve got to pre-bend them by hand,” Broeker says. “That adds a lot of time to the job.”
The tiles arrived at the site in bundles that contained pre-blended assortments of Slate Grey, Charcoal Grey, Red Cedar and Forest Green colors. That saved the time and effort of blending the colors during installation. “Just on shuffling and handling before the installation, it probably saved 20 percent on labor,” Broeker says. “The labor to install real slate is at least twice what it would be for artificial slate. We can nail gun artificial slate, whereas real slate, you’ve got to hand nail everything and you’ve got to be real careful how far you drive the nail.”
One of the challenging aspects of this project was the various curvatures of the roof. The surface curves outward at the base, slopes steeply upward, and curves inward near the top. The most complex curvature is at the base of the bell tower, where the roof bulges out. “The roof goes straight vertical, and the bell tower comes out lower and changes at a different pitch,” Broeker says. “In order to keep your vertical lines straight all the way across, there’s a lot of mathematics involved in keeping your slots straight, going up and down.” He explains that they adjusted both the tile exposures and the gaps between them to achieve the desired alignment.
The Sustainability of Synthetic Slate
InSpire’s literature lists three categories in which their simulated-slate roof tiles can qualify for between three and six credits toward LEED certification. Construction waste from trimmed tiles is completely recyclable. The tiles are also reusable if they are removed carefully. The light weight means that fewer trucks are needed to deliver the tiles, resulting in lower delivery costs and reduced vehicle emissions.
DaVinci’s website mentions several other sustainability benefits of its synthetic slate. Offering five different widths of tiles reduces the need for on-site trimming, which produces construction waste. Their product is also recyclable. They assert that their manufacturing process is more energy efficient than quarrying natural slate and uses less oil than the production of asphalt shingles. Furthermore, their literature says, “The petroleum content in our products is a by-product of gasoline refinement — one that in the past was simply burned off.”
Jim Diehl says his customers are increasingly interested in sustainability, and one of the best ways to provide that is a long-lasting, maintenance-free roof. “I think the application of this artificial slate is really great for churches,” he says. “They bring out the richness of the church, and are functional, sustainable and are aesthetically pleasing.”
Loretta Hall is a freelance writer concentrating on architecture, engineering and construction. A member of the Construction Writers Association, she is also certified as a Green Building Technical Professional.
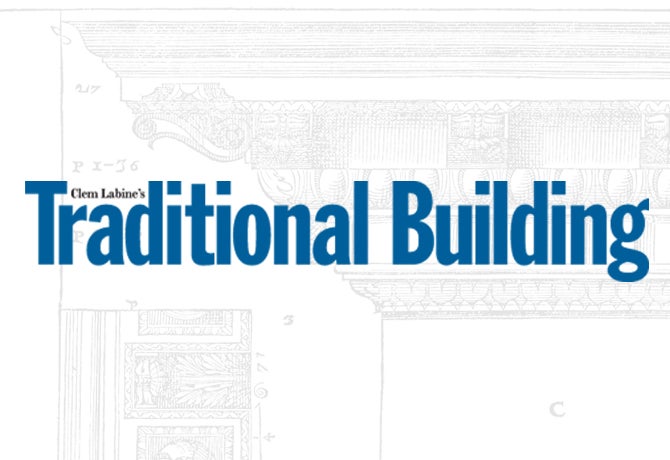
Loretta Hall is a freelance writer concentrating on architecture, engineering and construction. A member of the Construction Writers Association, she is also certified as a Green Building Technical Professional.